Typical applications for sealing cover films include packaging and labeling. These products provide an air interface to the back surface of structured elements such as sheetings, and can protect them from degradation. Often, these films are attached to a microsphere-coated base sheeting. They can also be used for bagging and packaging dried fruits and other similar products.
Sealing cover films can be opaque or light transmissive, and can have various properties, including sealant, film former, and opacity. They are typically attached to structured retroreflective sheetings using an embossing tool. Sealant may be used to enhance the integrity of the retroreflective sheeting, whereas film former may reduce the film's shrinkage. The film's properties are controlled by the film's composition, the film's thickness, and the type of coater.
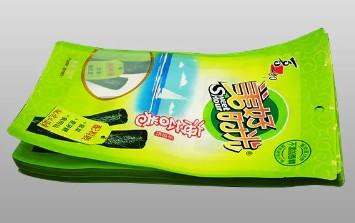
Sealing cover films are often attached using a heated embossing tool. In this process, a layer of adhesive (which may be solvent activated) is applied to the back side of the binder layer and a seal coat material (which may be organic, solvent-borne, or water-borne) is applied to the back surface of the cover film. The process typically causes indentations to form in the binder layer, and the cover film is attached to the indentations. This method creates a sealant that is non-pierceable and does not allow contamination to occur between wells.
The process can be accelerated by using a curing agent. The curing agent helps the seal coat to polymerize more rapidly. The thickness of the seal coat depends on the viscosity and the composition of the seal coat precursor. In addition, the thickness of the seal coat will vary depending on the application and desired final properties.
The bond between the adhesive and the binder layer is typically less than the bond between the cover film and the binder layer. The strength of the bond between the binder layer and the cover film is influenced by the bond between the binder layer and the microspheres 212 embedded in the binder layer. The fracture strength of the binder layer is also influenced by the bond strength between the binder layer and the cover film. In the present invention, the bond strength between the binder layer and cover film was tested using a Z-peel test. The bond strength was found to be significantly higher in back-coated samples than in control samples. However, the locus of failure was different between the coated and control samples. This locus was located between the adhesive and the cube-corner elements.
The thickness of the seal coat layer can vary depending on the viscosity of the seal coat precursor and the type of coater. If the film is to be opaque, it is preferred that the seal coat layer be applied over the back surface of the sheeting. If the film is to be transparent, it is preferred that the seal coat layer partially fill in the indentations created by the seal legs of the sheeting. The amount of the film former may also depend on the desired opacity of the seal coat layer.